All speed-related sports require a helmet. Classified according to human body parts the helmet is the first life-saving equipment. There are many types of helmets, different sports, different uses and different shapes, half helmets, full helmets, face helmets, cross-country helmets and so on. However, in terms of manufacturing procedures, they are basically the same. Knowing how the helmet is made can better enable us to purchase and use the helmet.
Tools/raw materials: Polycarbonate material Composite material Method/StepMaking EPS (expandable polyethylene) helmet lining: why choose EPS? There are three main points, which are cheap, light and easy to use. It's amazing; this kind of foaming material that can be used to make lunch boxes is a good head protection material. In fact, one of the differences between an ordinary helmet and a high-quality helmet is the quality of polyethylene. For example, some helmet manufacturers use the same polyethylene propylene material to make the entire lining, while others develop polyethylene lining with different thickness, strength and shape specifically for the purpose and shape. The latter means that each helmet must have its own mold and CAD design, which of course means cost.
How to make a helmet Make a polycarbonate helmet shell. The resin is injected into the helmet shell mold machine in a liquid state, and is formed by extrusion of the child and mother molds. Each helmet mold is also designed with CAD/CAM models for different sizes. The molds used to manufacture helmets have a life cycle, and each time a new helmet is launched, a batch of molds will be eliminated. From injection to molding, each helmet mold takes about 60 seconds, after which it enters the next step, grinding, spraying, and decals. Then install the mask, and perform anti-scratch and anti-fog treatment on the mask. Polishing, painting and carving treatment. One advantage of the polycarbonate helmet is that once the mold is completed, the mask and other moving parts can be directly installed, because all hole positions of the polycarbonate helmet are reserved during the molding process, and no subsequent drilling is required. Some manufacturers use mechanized processes in the helmet polishing process, while others maintain manual processing. After the surface is treated, the helmet will be painted and decals. The decals are designed and printed by the computer, and finished by manual. Finally, a helmet is basically finished by polishing. Assemble, pack and ship. After the appearance-treated helmet, various required parts, visors, face masks, etc. will be installed. At the same time, the final quality inspection of the staff will be accepted during this process, including thickness inspection of various parts, impact test sampling, etc., and finally packaging and transportation, We can buy it on the market.
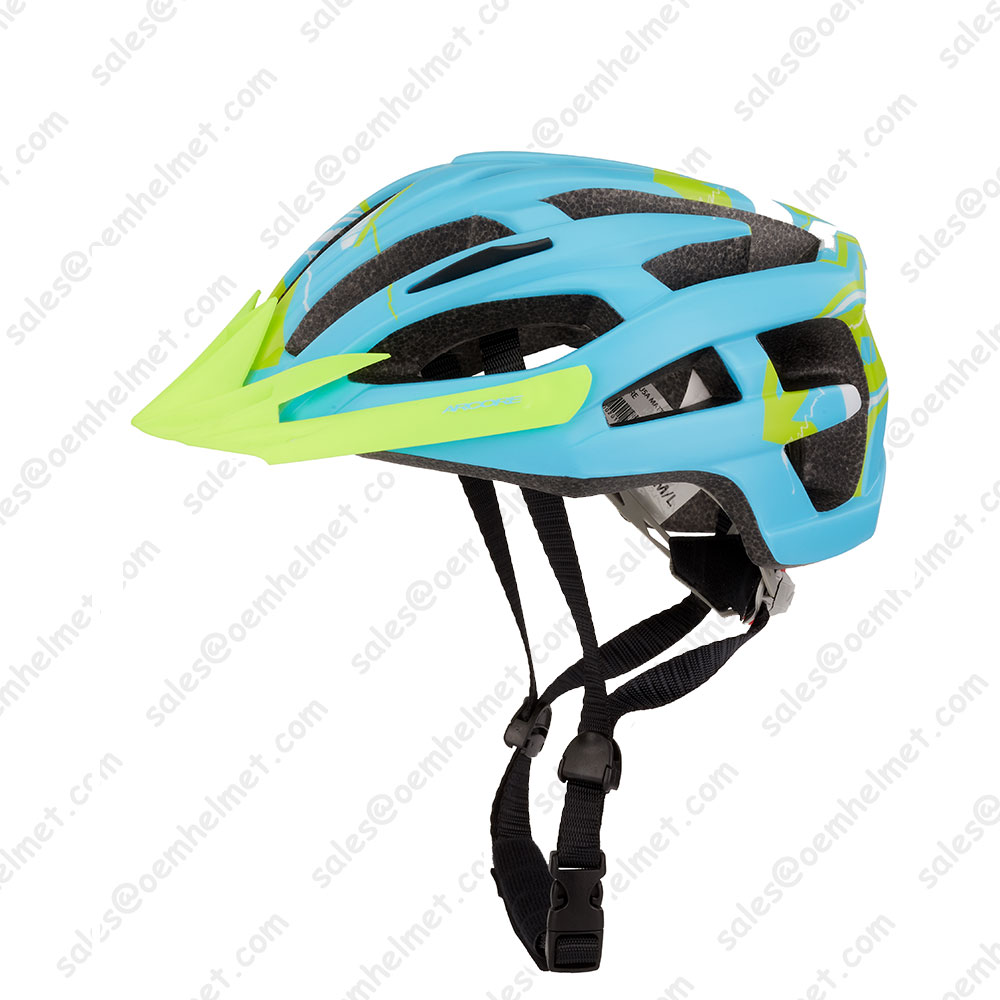
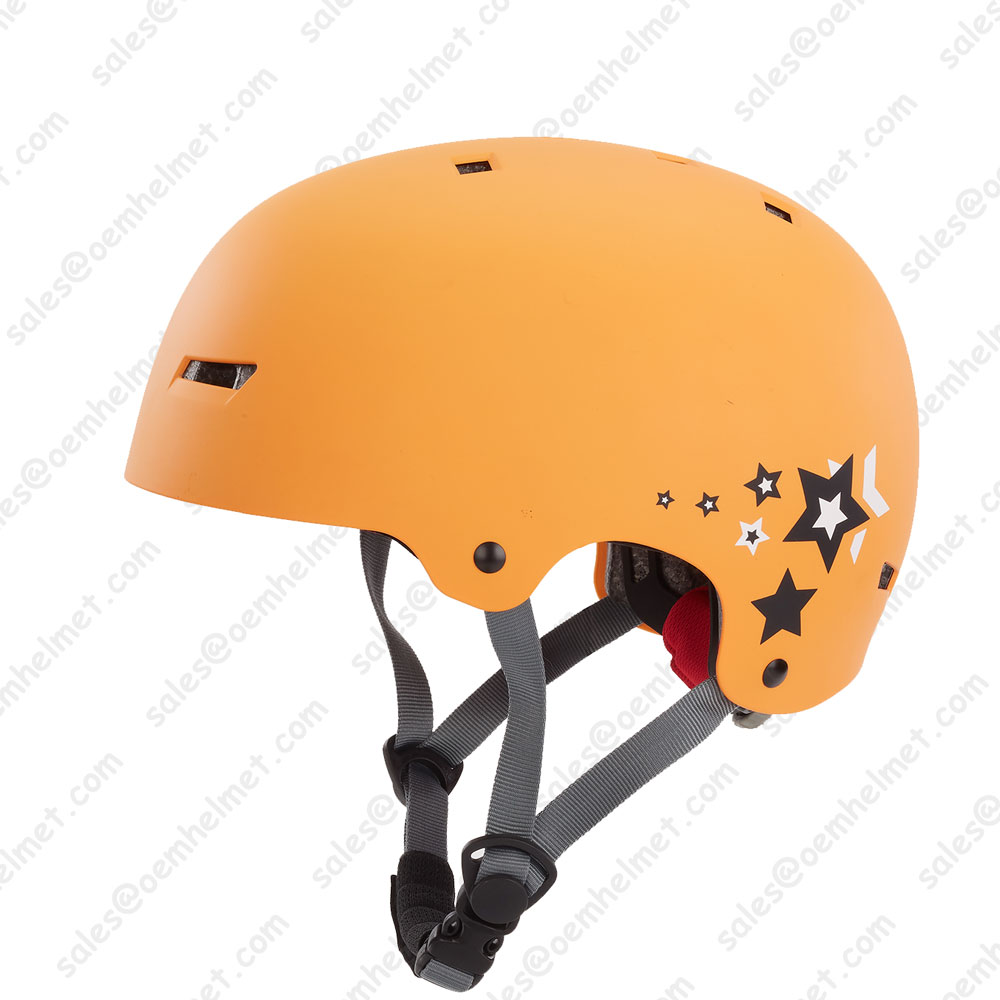
Comments